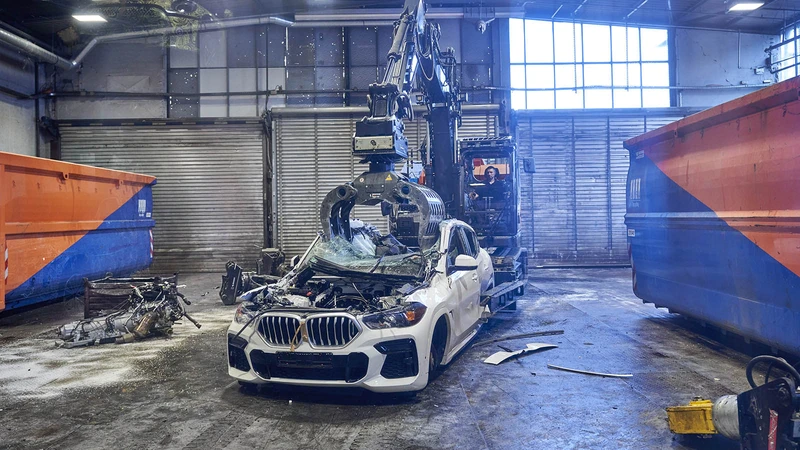
El fascinante mundo de los prototipos y las mulas de desarrollo en el mundo automotriz, da para escribir un libro. Es una etapa de ensayo y error, donde se están probando mil componentes antes de la certificación final. En una primera etapa, muchas de estas piezas se prueban de manera experimental en autos muy lejanos al producto final, los que pueden ser engendros creados solamente para suplir una estructura o para probar ciertas piezas. Se pueden tomar autos preexistentes, se recortan, se le sacan las insignias, se camuflan y se transforman en verdaderos laboratorios ambulantes.
En la medida que las piezas finales van siendo terminadas, estas mulas comienzan a dar pie a prototipos de preserie cercanos al modelo final. A veces, estos se fabrican a mano o a veces en una partida de prueba en la línea de ensamblaje. Y para los que hemos tenido el privilegio de ir a plantas automotrices y centros de desarrollo, estos autos no son ni 10 o 20, sino que cientos de unidades que terminan en departamentos de acústica, interferencia, seguridad, pruebas mecánicas, talleres de diseño interior y exterior, pruebas en ruta y así.
Los modelos finales de preserie, cuando ya están casi listos para iniciar la fabricación en masa, terminan en autoshows y en uso por los departamentos de marketing y publicidad, así como también son exportados para hacer pruebas de homologación en distintos mercados. Pero ninguno de estos autos está visado para su comercialización final, por ende, cualquier auto de preproducción, por terminado y completo que esté, debe ser destruido.
¿Por qué? Por la sencilla razón de que se fabricaron bajo un protocolo experimental de pruebas, por ende puede haber sido intervenido por ingenieros o puede aun estar sujeto a verificaciones finales. Además, muchos de estos autos no siempre tienen un numero VIN asignado. En síntesis, la marca no va a poner las manos al fuego por un auto que no salió íntegramente de la planta de montaje como un producto acabado y certificado.
Cómo destruyes el auto, queda a criterio de las marcas. Los más creativos han aprovechado estas instancias para anticipar el modelo en alguna pieza publicitaria o película. Un caso moderno, fue una de las últimas películas de James Bond, donde 007 es perseguido por una horda de nuevos Land Rover Defender; todas esas unidades eran de pre serie, por lo que a nadie le iba a doler si eran chocadas. Otras marcas como BMW, prefieren el reciclaje.
30 años desmantelando prototipos
El Centro de Reciclaje y Desmantelamiento (RDC) de BMW Group comenzó casi como una chatarrería propia de la marca, pero con el tiempo fue transformándose en un "centro de excelencia" para el reciclaje de autos, acumulando experiencia que les permite incluso ponerse a la vanguardia de futuras regulaciones medioambientales.
Es aquí donde, aunque te duela, vienen a parar prototipos de pre serie terminados de todos los autos del grupo. Imagina un M5 o un XM y hasta un Serie 7, perfectamente terminados y que podrían venderse como autos nuevos, siendo acarreados por grúas y camiones para ser desarmados y destruidos bajo un medido y estructurado proceso que permite identificar lo que se puede reutilizar, de lo que se puede reciclar y de lo que va a ser eliminado.
BMW Group fue fundamental en la creación de la plataforma IDIS (Sistema Internacional de Información de Desmontaje), en la que el RDC publica sus datos y hallazgos. Estos están disponibles de forma gratuita para empresas de reciclaje de todo el mundo. Alrededor de 3.000 organizaciones en 32 países actualmente utilizan la base de datos conjunta de reciclaje para aprender cómo desmontar componentes reciclables de manera rentable y recuperar materiales valiosos de manera eficiente.
El proceso
El reciclaje de vehículos en el RDC comienza con la liberación controlada de los sistemas de retención y el bombeo de todos los fluidos. Con esto nos referimos a los sistemas de accionamiento pirotécnicos en los cinturones de seguridad y airbags, el aire de los amortiguadores, entre otros, todo con procesos o dispositivos diseñados para aquellas tareas.
Durante la fase de desmantelamiento subsiguiente, el enfoque inicial es el reciclaje de componentes individuales. Los componentes funcionales que se encuentren en perfectas condiciones y con estado de serie no se desechan, sino que se pasan a distribuidores registrados para su reventa como repuestos autorizados. Durante el desmantelamiento mecánico del resto del vehículo, ciertos materiales, como el cobre contenido en los ramales de cables, se separan utilizando maquinaria especialmente diseñada. Una vez que se han retirado el bloque del motor y la transmisión, el vehículo restante se prensa y se tritura en una instalación de reciclaje externa.
El desmantelamiento dirigido de metales asegura que la chatarra de hoy se convierta en la materia prima de mañana, en la mayor medida posible y con la mejor calidad posible. Esto no solo es importante desde el punto de vista ambiental, sino también desde el punto de vista financiero: al igual que el cobre, los metales utilizados en el tren motriz generan ingresos particularmente altos. El desmantelamiento separado del convertidor catalítico también es económicamente eficiente debido a los valiosos metales preciosos que contiene.
Los beneficios
Gracias a todo lo que logra el RDC, es que BMW ha podido participar de otras instancias de investigación y desarrollo. Por ejemplo, participan del proyecto de investigación Car2Car, subvencionado por el gobierno federal alemán, lo que ha permitido impulsar la fabricación de autos con más materiales reciclables y saber exactamente qué es lo que más se recicla y que es lo que podría tener un potencial reciclable, así como el estudio de procesos de desmantelamiento semiautomatizados para separar este tipo de materiales.
Esto también ha decantado en otras iniciativas, como el uso de mono-materiales que son más fáciles de reciclar que los materiales o polímeros compuestos y el uso de procesos de ensamblaje que permitan también métodos más efectivos de desmantelamiento; cambiar los adhesivos en ciertas zonas por otro tipo de uniones.
La siguiente frontera son las baterías de los autos eléctricos, que es donde el RDC está concentrando todos sus recursos, para así aportar con nuevas ideas y soluciones a otros centros de reciclaje más masivos.